Recognizing the Fundamentals and Applications of Plastic Extrusion in Modern Manufacturing
In the realm of contemporary production, the strategy of plastic extrusion plays an instrumental duty. Unwinding the fundamentals of this procedure reveals the real versatility and capacity of plastic extrusion.
The Principles of Plastic Extrusion Refine
While it might appear complex, the basics of the plastic extrusion procedure are based on relatively uncomplicated principles. It is a production procedure wherein plastic is melted and after that shaped right into a continual profile through a die. The plastic extrusion procedure is extensively made use of in numerous markets due to its cost-effectiveness, convenience, and effectiveness.
Different Kinds Of Plastic Extrusion Techniques
Structure upon the fundamental understanding of the plastic extrusion process, it is essential to discover the different techniques involved in this production method. In comparison, sheet extrusion produces huge, flat sheets of plastic, which are commonly more processed into items such as food packaging, shower curtains, and car components. Recognizing these techniques is vital to utilizing plastic extrusion efficiently in modern-day manufacturing.
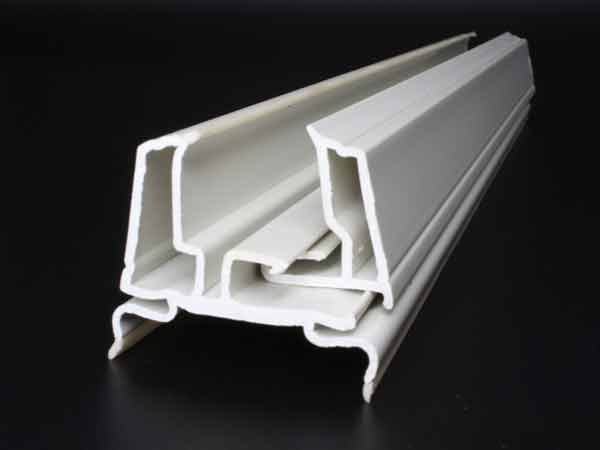
The Duty of Plastic Extrusion in the Automotive Sector
An overwhelming bulk of components in modern automobiles are products of the plastic extrusion process. Plastic extrusion is primarily utilized in the manufacturing of various automobile parts such as bumpers, grills, door panels, and control panel trim. Hence, plastic extrusion plays a critical function in auto production.
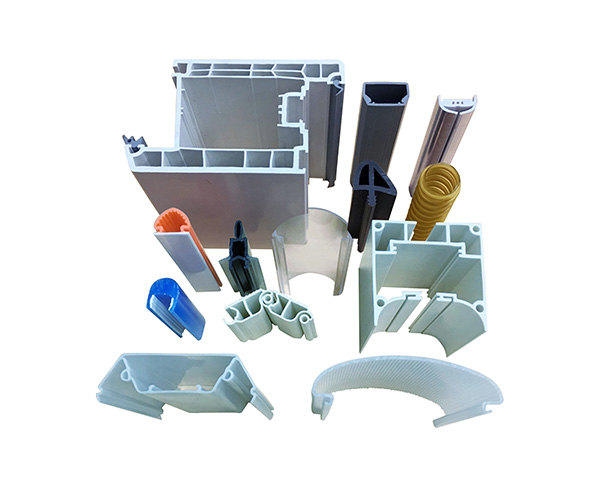
Applications of Plastic Extrusion in Customer Product Manufacturing
Past its considerable effect on the automotive market, plastic extrusion shows just as effective in the realm of customer goods producing. This process is crucial in developing a large range of items, from food product packaging to house home appliances, toys, and even medical tools. The versatility of plastic extrusion allows suppliers to create and generate complicated sizes and shapes why not check here with high accuracy and efficiency. In addition, as a result of the recyclability of lots of plastics, extruded elements can be reprocessed, decreasing Visit This Link waste and price. The flexibility, versatility, and cost-effectiveness of plastic extrusion make it a preferred option for numerous customer products manufacturers, contributing significantly to the market's development and technology. The ecological implications of this widespread use need cautious factor to consider, a subject to be talked about better in the succeeding area.
Ecological Impact and Sustainability in Plastic Extrusion
The pervasive use plastic extrusion in manufacturing welcomes analysis of its eco-friendly effects. As a process that often makes use of non-biodegradable products, the environmental effect can be significant. Power usage, waste production, and carbon emissions are all problems. Market advancements are raising sustainability. Reliable equipment reduces power use, while waste management systems reuse scrap plastic, lowering resources demands. In addition, the development of biodegradable plastics go to this web-site uses a much more eco pleasant option. Despite these improvements, additionally advancement is needed to minimize the environmental footprint of plastic extrusion. As society leans in the direction of sustainability, makers should adapt to stay sensible, emphasizing the importance of constant study and innovation in this field.
Conclusion
In conclusion, plastic extrusion plays an essential duty in contemporary manufacturing, especially in the automobile and consumer items sectors. Recognizing the basics of this process is essential to maximizing its applications and advantages.

The plastic extrusion process is extensively used in various sectors due to its cost-effectiveness, flexibility, and efficiency.
Building upon the basic understanding of the plastic extrusion procedure, it is necessary to discover the various strategies included in this manufacturing approach. plastic extrusion. In comparison, sheet extrusion produces big, flat sheets of plastic, which are generally further processed into products such as food product packaging, shower curtains, and cars and truck components.An overwhelming bulk of components in modern-day automobiles are products of the plastic extrusion procedure
Comments on “Plastic extrusion for creating even, premium parts”